"Creep is the slow plastic deformation of metals under constant stresses (or) under prolonged loading usually at high temperatures". We should particularly take the creep into account when designing the I.C Engines, Turbines, and Boilers.
Creep at lower temperature is known as 'Low temperature creep' and can occur in load pipes, roofing's, glass as well as in metal bearings. Creep at high temperature is known as 'High temperature creep'.
Where creep is important?
In design, we seek materials that will carry the design loads without failure for the design life at the service temperature. Creep is a very important consideration in design in three types of high temperature applications:
1. Displacement-limited applications in which precise dimensions or small clearances must be maintained such as in turbine rotors in jet engines. (Figure 1a).
2. Rupture-limited applications in which precise dimensions are not essentials but fracture must be avoided such as in high pressure steam tubes and pipes. (Figure 1b)
3.Stress-relaxation-limited applications in which an initial tension relaxes with time such as in suspended cables and tightened bolts (Figure 1c).
In these types of applications, design engineers should consider creep deformation and its dependence on time and temperature. Many mechanical systems and components like turbines , steam boilers, and reactors operate at high temperatures and high pressure so creep properties for the materials used must be determined.
The main objective of the creep test is to measure how a given metal or an alloy will perform under constant load, at elevated temperatures. In the creep test, a tensile specimen (with similar dimensions as a tensile test specimen) is subjected to a constant load inside an electric furnace where the specimen is heated to specific temperature and the temperature is maintained constant. Figure illustrate a simple setup for creep testing. The resulting deformation or strain is measured and plotted as a function of elapsed time. that graph shows a schematic creep curve for a metal tested at constant load until rupture. Metals, polymers, and ceramics all show similar strain-time behaviors. The instantaneous strain is purely elastic and can be calculated by, equation 1 with E as the modulus at the testing, temperature. The creep curve in Figure demonstrates three regions of strain-time behavior:
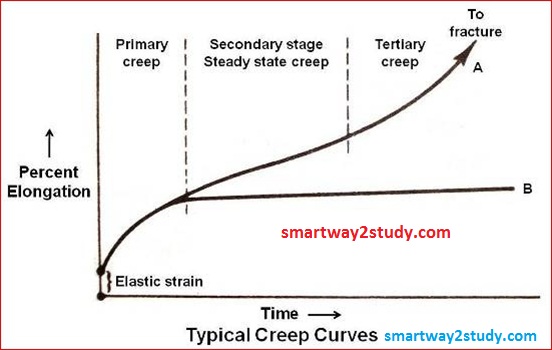
1. Primary creep where the rate of change of strain (creep rate=∆ε/∆t) decreases with time due to strain hardening of the material.
2. Steady-State creep where the strain increases linearly with time. From design point of view, this region is the most important one for parts designed for long service life because it comprises the longest creep duration. The main creep test result is the slope of this region which is known as the steady state creep rate (′εs). During this stage of creep, thee is a balance between strain hardening due to deformation and softening due to recovery processes similar to those occurring during the annealing of metals at elevated temperature.
3. Tertiary-creep Where the strain increases rapidly until failure or rupture. The time to failure is often called as the time to rupture lifetime (tr). This parameter is an important consideration in designing against creep for parts intended for short-life applications. To determine the rupture lifetime, the creep test must be conducted to the point of failure. Such test is also known as the stress rupture test (or) Creep rupture test.
Testing either at higher stresses or higher temperature will increase the steady state creep rate (′εs ) and reduces the rupture lifetime (tr) as illustrated. Note that the strain is constant and independent of time for temperatures below 0.4 Tm. Experiments suggest that the combined influence of applied stress and temperature on the steady state creep rate can be represented as
ε′s = K σn exp (-Qc/RT) --(2)
where, K is the creep constant,
Qc is the activation energy for creep,
n is the creep exponent ( lies b/n 3 & 8 ) and,
R is the gas constant.
The values of the three constants K, Qc and n describe the creep of a given material and if they are known, you can calculate the steady state creep rate at any temperature and stress using equation 2. However, these parameters vary from material to material, and have to be determined experimentally.
Factors affecting creep:
(1) load: Creep strain varies with the applied load. With applied stress (load) creep strain rate increases.
(2) Temperature: At high temperature creep rate increases. At higher temperatures materials undergoes more creep strain compared to one at lower temperatures.
(3) Composition: Pure metals with high melting points and compact atomic structure generally exhibit more creep resistance at high temperature. By allowing the pure metals with suitable elements, the creep resistance can be increased considerably.
(4) Grain size: Grain Size is the major factor in creep. Generally coarse grained materials exhibit better creep resistance than fine grain. At lower temperatures a material with a smaller grain size has a slower creep rate. Coarse grains show higher creep strain.